Shoes
Northampton shoemaking - factory life
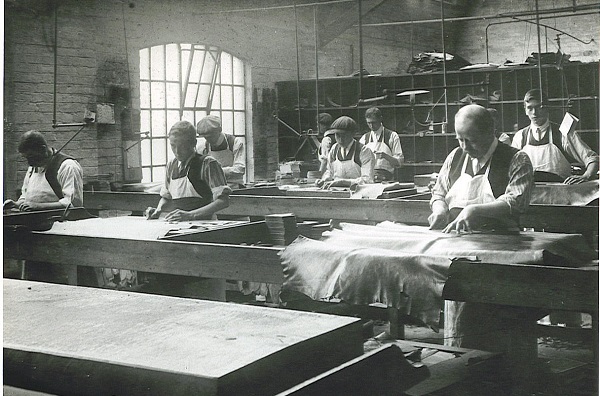
Clicking room, unknown shoe factory in Kettering, about.1900
Mechanisation
Traditionally, shoemakers worked alone, with a wife, or in small groups. As the changeover to a mechanised industry occurred it was increasingly difficult for the shoemaker to own the modern tools of the trade. He therefore did not have the means to work under his own terms and became a member of the industrial working class. The following adult roles in 1895 (save for the women in the closing room) would have typically earned in the region of 28 shillings per week although this would vary according to the individuals output as all in the factory were paid ‘by the piece’. A young lad starting an apprenticeship (in the clicking room for example) would take home less than a quarter of this for a 54 hour week which was the standard working hours throughout the factory. Throughout these mechanised times from the end of the 1850s onwards boot and shoemaking traditionally became divided into five main departments or rooms:
The clickers
The clickers became known as the elite or the ‘gentlemen’ of shoemakers. Their role involved cutting out the shoe uppers from the precious fine leathers using knives with very curved and sharply pointed blades. This highly skilled role became known as ‘clicking’ as the concentration required to carry out the task required silence – the only noise in the clicking room would be the click, click of blade piercing leather and the wooden cutting block underneath.
The closers
The wife of the traditional shoemaker undertook the task of closing - sewing the uppers together - and the closing room of the factory too became a generally female environment. The closing room received the uppers after the clickers and here they went through the hands of around thirty operatives in order that the numerous processes required before stitching be completed. For the standard factory hours the women in the closing room would have earned between nine and 18 shillings a week, being paid ‘by the piece’. Processes included eyeletting, skiving and punched decoration.
The closing room at J. Sears & Co (Trueform Boot Co) Ltd, Northampton, about 1900
![]() |
The rough stuff room
The ‘rough stuff’ room refers to the area of the factory in which some of the most important parts of the soles are cut such as the heels and the sole, together with other parts of the shoe that cannot be seen such as the welts - all of these components commonly being called bottom stock. The name ‘rough stuff’ might not clearly imply the skill involved in creating the foundation of the shoe, but skill was required.
The rough stuff room at The Mounts shoe factory, Northampton, about 1900.
![]() |
The making (or lasting) room
Here the soles and the uppers are joined together using a foot shaped last. First the components are tacked together and the dampened uppers and the sole are stretched over the last and joined, and finally the heel is added. Large machines known as a pulling over machines held the upper fast whilst a stitching machine attached the sole to the upper. The ‘Blake Sewer’ was the key for the mechanisation of the industry. The machine was so large, expensive and efficient that it gave the death knell to any remaining makers of hand stitched shoes outside of the factories. These were unable to invest in such a large piece of equipment and as such were finally squeezed out of business.
The making room at the Mounts shoe factory, Northampton, about 1900
![]() |
The finishers
Finishers undertook the process of trimming, smoothing and finally colouring and polishing the soles and heels. The finishing processes were numerous and increasingly complex during this time and as such the finishing room was one of the last areas to become mechanised. By the turn of the century the finishing room had heel and edge finishing machines, edge setting machines, bottom scouring machines and heel and bottom padding machines. All of these replaced processes that had previously been completed by hand.
The packing room at an unknown shoe factory, Kettering, about 1900.
![]() |